Injection molding is one of the most commonly used production processes for plastics. This is correct because it provides a viable solution for mass production of high-quality injection molded automotive parts from a variety of polymers. In the automotive industry, consistency, safety and quality are crucial, and automotive plastic injection molding is an important manufacturing process.
Advantages of Injection Molding in Automotive Applications
Injection molding is a mature production process. Automobile mold manufacturers inject molten plastic materials into the mold cavity. The melted plastic is then cooled and hardened, and the manufacturer extracts the finished product. Although the mold design process is critical and challenging (poorly designed molds can cause defects), injection molding itself is a reliable method of producing solid plastic parts with high quality finishes.
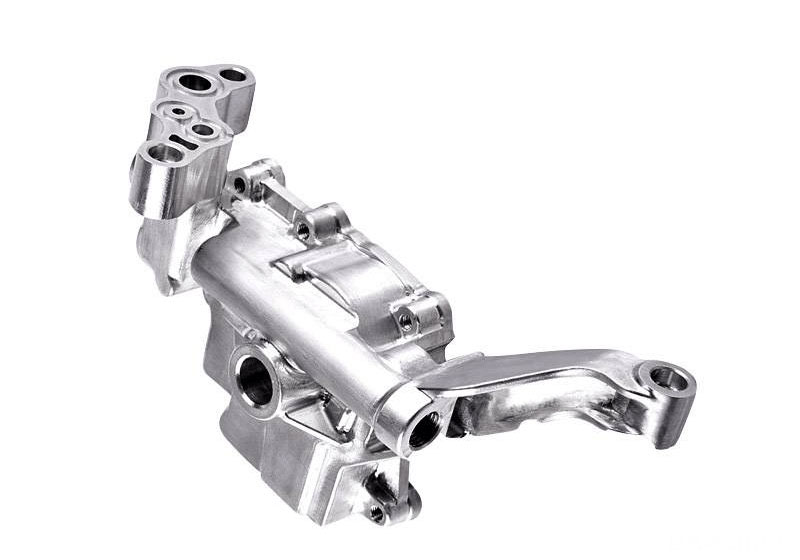
The following are the reasons why this process is beneficial to the production of automotive plastic parts:
1. Repeatability
In the automotive industry, repeatability – or the ability to consistently produce the same parts – is critical. Because automotive plastic injection molding usually depends on a solid metal mold, the final molded automotive parts produced with this mold are actually the same. Some factors will affect injection molding, but if the mold has good design and finishing, injection molding is a highly repeatable process.
2. Scale and cost
Due to the cost of the mold, the manufacturing process of the injection mold may be an expensive process. However, it is still a highly scalable process, and its total cost will decrease as manufacturers manufacture more parts. For mass production applications, injection molding is therefore beneficial to manufacturers. However, for anything that is not mass produced, injection mold costs may inhibit the cost efficiency of the process.
3. Color options
In automotive plastic injection molding, it is easy to modify the color of molded automotive parts to adapt to the color scheme of vehicles. Unlike other processes, injection molding allows you to mix dye with raw material particles before manufacturing begins. This will produce a solid, consistent colouring after forming without painting or colouring.
4. Material availability
A significant advantage of using injection molding in automobile production is that the process can be compatible with a wide range of rigid, flexible and rubber plastics. Manufacturers use various polymers for various applications in the automotive industry, including ABS, polypropylene, acrylic acid, acetal, nylon, polycarbonate, etc.
5. High precision and surface finish
Injection molding is an ideal choice for producing plastic parts with relatively simple geometric shapes, which can achieve high surface finish quality. Manufacturers have many surface treatment options when producing parts, including various surface textures (such as smooth, rough, or matte) that are directly applied to molds rather than molded parts. However, different plastic materials will also affect the final surface finish.
6. Rapid prototyping using quick tools
Although auto manufacturers widely use injection molding to mass produce auto parts, they also use it as a prototyping tool. By using rapid tooling to manufacture fast, low-cost aluminum molds – usually through additive manufacturing or CNC processing – auto mold manufacturers can complete the production of small batches of prototype auto parts faster than traditional (steel) molds.
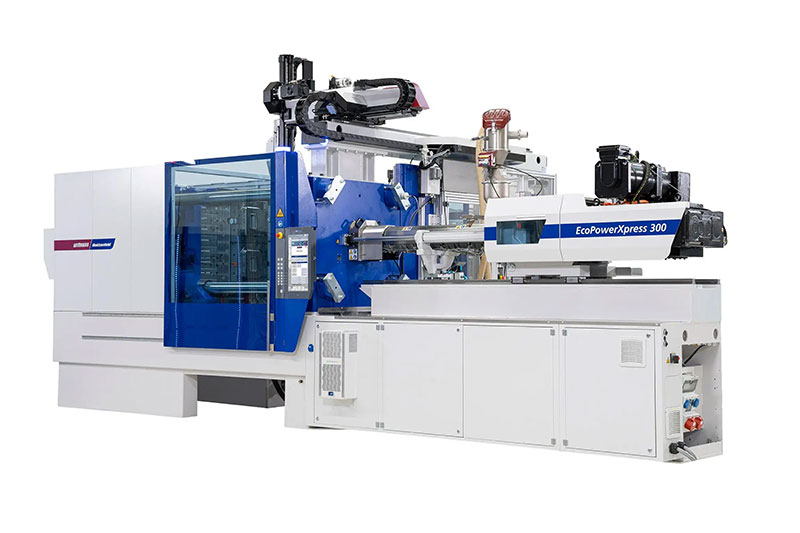
Production Application of Automobile Injection Molding
In the automotive field, injection molding is one of the main methods used by manufacturers to form plastic parts. However, it is difficult to list the plastic parts in the vehicles produced by injection molding, so we will know some main parts.
1. Components under the hood
In the past two decades or so, many underhood parts made of metal by manufacturers have been converted to plastic. For these applications, sturdy polymers such as ABS, nylon, and PET are common. However, manufacturers now use injection molding to manufacture parts such as cylinder head covers and oil pans. Compared with metal parts, this method has lower weight and cost.
2. External components
Injection molding is a mature process for many automotive external parts, including fenders, grilles, bumpers, door panels, floor rails, lampshades, etc. Splash shields are a good example of the durability of injection molded parts. In addition, components that protect the vehicle from road debris and minimize splashes are usually made of rubber or other durable and flexible materials.
3. Internal components
Manufacturers also use automotive plastic injection molding to produce many automotive interior parts. They include instrument components, interior surfaces, instrument panel panels, door handles, glove boxes, vents, etc. In addition, they use injection molding to produce decorative plastic components.
Alternative to Injection Molding for Low Cost Automobile Prototypes
In many cases, molded plastic can be used as a substitute for metal. Previously, manufacturers only used metal to manufacture items such as brackets, trunk lids, seat belt modules and airbag containers. Nowadays, injection molding is the preferred production method for these plastics.
On the other hand, manufacturers can sometimes replace molded plastic parts with 3D printed plastic car parts. This is particularly true in prototyping, where there is less demand for extreme durability or smooth surface finish. Many moldable plastics can be used as FDM 3D printer filaments or as nylon SLS 3D printer powders. Some professional and high-temperature 3D printers can also print reinforced composites for high-strength parts.
For one-time prototypes, especially non mechanical parts, 3D printing may be a cost-effective alternative to molding. Because there is no mold cost, the production price is not so high.
In some cases, manufacturers may even use 3D printing for a few end use automotive parts. They may use SLM 3D printing to manufacture fluid handling components such as valves (usually not injection molded). However, another option is to use SLS3D printing to manufacture parts such as bumpers, decorations and windcoats, which are sometimes injection molded.