CNC machining usually refers to CNC precision machining, CNC Turning machining(cnc lathe), CNC milling machining , CNC turning milling machining, etc.
Features of CNC processing of Shenzhen industrial cncprotolab:
- High degree of automation and high production efficiency. Except for blank clamping,all other processing procedures can be completed by CNC machine tools. If the automatic loading and unloading mode is combined, it is a basic part of the unmanned factory. CNC processing reduces the labor of the operator, improves the working conditions, eliminates the marking, multiple clamping and positioning, detection and other processes and auxiliary operations, and effectively improves the production efficiency.
- The processing precision is high, the quality is stable, and the processing dimension precision is between d0.005-0.01mm, which is not affected by the complexity of the parts. Because most operations are automatically completed by the machine, the size of batch parts is improved, and the position detection device is also used on the precision controlled machine tool, which further improves the precision of precision CNC processing.
- Adaptability to CNC machining objects. When changing the processing object, in addition to changing the tool and solving the blank clamping method, only reprogramming is required without other complex adjustments, which shortens the production preparation cycle.
- CNC machining has two main characteristics: first, it can greatly improve the machining accuracy, including the machining quality accuracy and the machining time error accuracy; The second is the repeatability of processing quality, which can stabilize the processing quality and maintain the quality of processed parts.
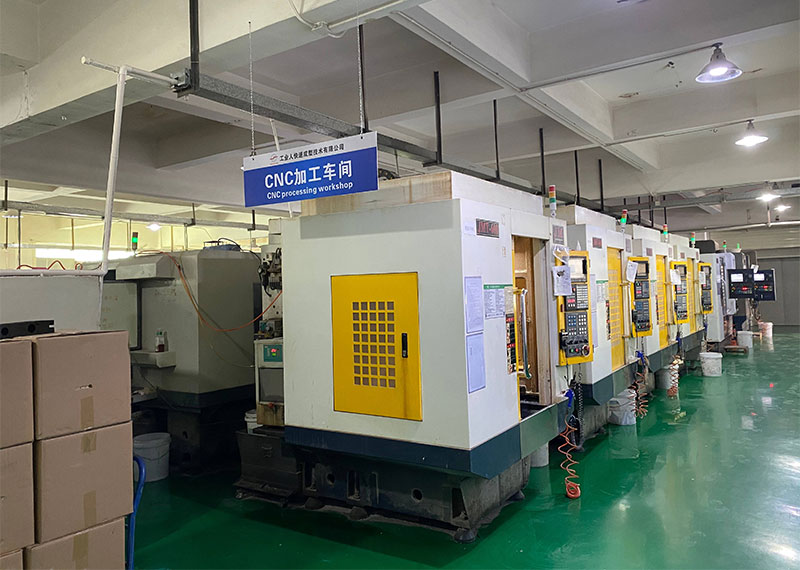
In CNC machining, we should improve the operation according to these characteristics of CNC machining to better improve the machining efficiency and quality. Machining technology of mechanical parts refers to the process of changing the size or performance of machined parts through a kind of mechanical equipment. According to the different processing methods, it can be divided into cutting and pressure processing.
The machining methods of mechanical parts mainly include turning, pliers, milling,planing, inserting, grinding, drilling, boring, punching, sawing, etc.
It can also include wire cutting, casting, forging, electric corrosion, powder processing, electroplating, various heat treatment, etc.
- Trolley: vertical lathe, horizontal lathe, new equipment: CNC lathe, mainly for processing revolving bodies,
- Milling: there are vertical milling and horizontal milling. The new equipment includes CNC milling, also called machining center, which mainly processes grooves and straight surfaces. Of course, it can also process surfaces, using two or three axis l++++inkage.
- Cutting: linear surface of main machining shape, the surface roughness machined under normal conditions is not as high as that of milling machine.
- Grinding: there are surface grinding, cylindrical grinding, internal hole grinding, tool grinding, etc., high-precision single-sided processing, and the surface roughness of the workpiece to be processed is particularly high.
- Drilling: hole processing
- Boring: It mainly uses a boring cutter or a blade to bore the inner hole, process holes with larger diameter and higher accuracy, and process larger workpiece shapes. There are many ways to process holes, such as CNC machining, wire cutting, etc.
- Punching: It is mainly processed by punching and forming CNC, and can punch round holes or special-shaped holes.
- Sawing: It is mainly used for cutting and processing with a sawing machine, and is commonly used for cutting sequence.
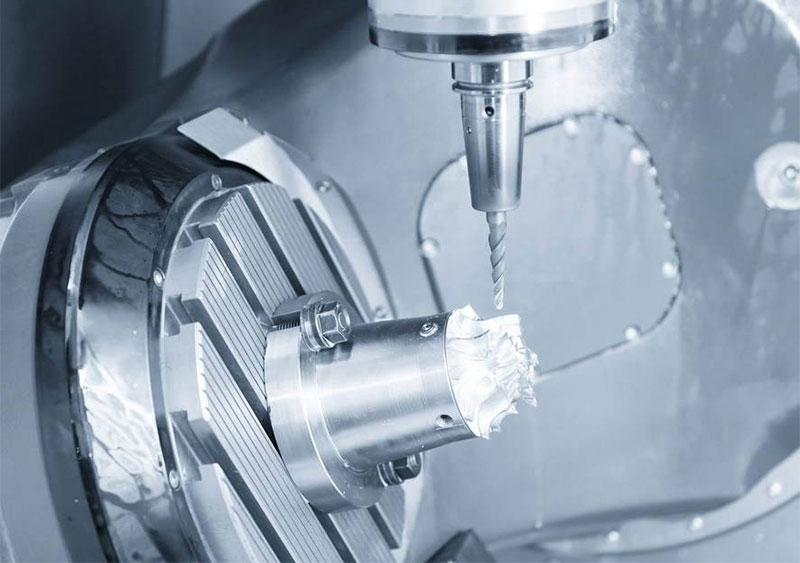
A machine is composed of several precision parts. Without these parts, the machine would not be complete.
CNC machining refers to machining with CNC machining tools. CNC indexing control machine tools are programmed and controlled by CNC processing language, usually G code. G code language tells CNC machine tools which rectangular coordinate position to process tools,and controls the feed speed of tools and spindle speed, as well as the role of tools in changing coolant and coolant. Compared with manual machining tools, CNC machining has great advantages. For example, the parts produced are very accurate and repeatable; CNC machining can produce parts with complex shapes that cannot be completed by manual machining.
CNC machining technology is now widely promoted. Most machining workshops have CNC processing capability. The common CNC machining methods in typical machining workshops include CNC milling, CNC lathe and CNC wire EDM. The tools used for CNC milling are called CNC milling machines or CNC machining centers.
The lathe for CNC turning is called CNC turning center. CNC machining G code can be programmed manually, but the machining workshop usually uses CAM “Computer Aided Manufacturing” software to automatically read CAD “Computer Aided Design” files and generate G code program to control the CNC machine tool. The lathe for CNC turning is called CNC turning center. CNC machining G code can be programmed manually, but the machining workshop usually uses CAM “Computer Aided Manufacturing” software to automatically read CAD “Computer Aided Design” files and generate G code program to control the CNC machine tool. The lathe for CNC turning is called CNC turning center.
CNC machining G code can be programmed manually, but the machining workshop usually uses CAM
“Computer Aided Manufacturing” software to automatically read CAD “Computer Aided Design” files and generate G code program to control the CNC machine tool.
CNC machining has the following advantages:
- The number of tooling is greatly reduced, and complex tooling is not required forprocessing parts with complex shapes. If you want to change the shape and size of the part, you only need to modify the part processing program, which is applicable to the development and modification of new products.
- The processing quality is stable, the processing precision is high, and the repetition precision is high, which is suitable for the processing requirements of aircraft.
- In the case of multi variety and small batch production, CNC processing is more efficient, which can reduce the time for production preparation, machine tool adjustment and process inspection, and reduce the cutting time due to the use of good cutting amount of ZUI.
- It can process complex profiles that are difficult to process by conventional methods, and even some processing parts that are difficult to observe.
The disadvantage of CNC machining is that the cost of machine tools and equipment is expensive and the level of maintenance personnel is high.
CNC processing is decoded by the computer to make the machine move and process parts. The blanks are processed into semi-finished products by cutting tools.