When you hear about precision CNC machining, what do you think of? CNC processing is not all “precision”? In a sense, yes. CNC machining enables you to manufacture a large number of very precise parts relatively quickly. However, it goes far beyond that.An important factor in precision machining is the accuracy rate, that is, the degree of precision.
Fine CNC machining is sometimes considered to mean that the parts manufactured are well within the specifications/geometry of the intended design. Technically speaking, this is not wrong, but the more accurate statement is accuracy. CNC machines are very capable of producing parts that are accurate enough for many applications, but sometimes not enough.
When you add precision to the mix, you can take it to a new level. This brings us the real question: What is precision machining? Precision and accuracy are often confused and used interchangeably. Both are indeed related to quality, but each has its own unique meaning. Accuracy refers to approaching or completely approaching the target value (many people think this is also the definition of precision). Accuracy is actually the ability to replicate consistent parts on a large number of production cells.
The key is “mass production unit”. Precision machining refers to multiple or multiple units. You can have an accurate part, but you must have many parts that need to be measured and compared to be accurate. For example, if someone asks to use precision CNC machining to create a single part, it is counter intuitive, because “precision” in machining will involve multiple parts.
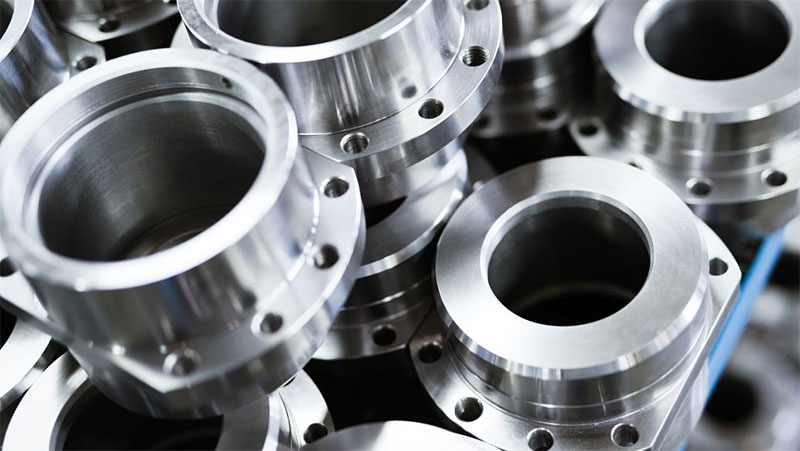
How do you know if your processes and parts are accurate?
Measuring system! Your measurement system is an integral part of measuring and determining part quality and accuracy. When you want to improve the process, it is important to be able to identify and measure any problems. This can help you identify the source of the problem or error and how to optimize it.
The first step is to ensure that your measurement system is good enough. Does it accurately measure your parts again and again? One way to check this is to use instrument parts and calibration to ensure that your measurement system is working properly. A measuring tool part is a part that is machined to a known value extremely accurately.
Some common processes used in development to find any measurement errors are GR&R and MSA. It is important to follow these because they will help you collect good data that can be used to identify errors in the measurement system or part.
MSA stands for measurement system analysis. By performing MSA, you can determine where the changes in measurements come from. Is your measurement system consistent and reliable? Does the person making the measurement consistently do so? Are your parts manufactured with minimal change? These three error sources will lead to greater changes in measurement. If you identify a variation that results in a significantly larger proportion, you can solve the problem and know that you are getting good measurements.
GR&R represents instrument repeatability and reproducibility. This is a commonly used MSA type. Repeatability refers to the ability of the operator to obtain the same measurement results repeatedly (on the same part). Reproducibility is the ability of another person to obtain the same measurement again and again. By identifying a person’s measurements and differences between people, you can identify differences between actual parts and parts.
To perform GR&R, you need 10 parts and 3 people to measure the parts. Each person will measure each part 10 times. With the result data, you can conduct a lot of analysis to analyze your measurement system. As mentioned earlier, you can calculate the components of variation: repeatability, reproducibility, operator variation, and variation between components. You can view Xbar or R control charts, which are graphical representations of operator changes. In short, there are many ways to view the data and determine whether your measurements are accurate.
Identifying these different sources of variation is very important for improving the accuracy of CNC machining process and parts.
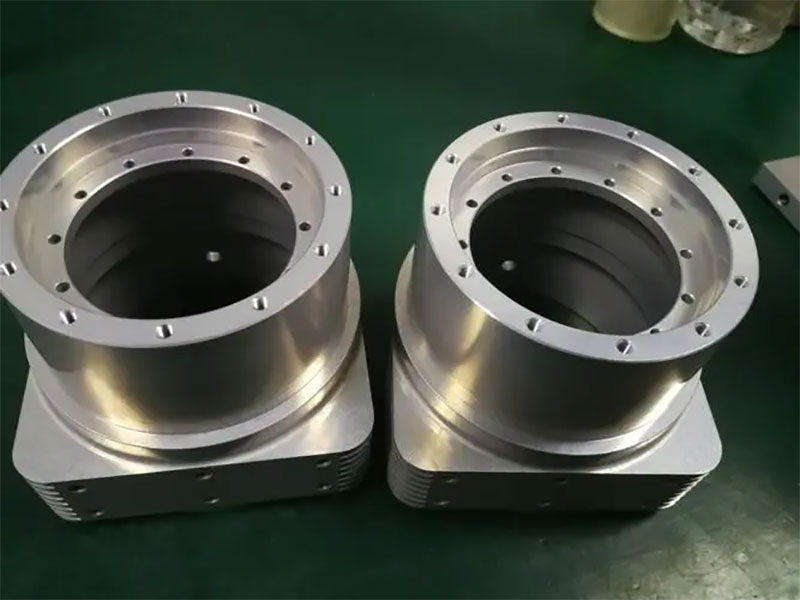
How to improve the accuracy of CNC machining process?
The first step is to consider your design from the perspective of DFM. Many DFM principles will also help improve part accuracy. The five design parameters to be noted are geometry, material, tolerance, part size, and appearance. The workload drivers of these parameters are also related to precision – the more work required to process these parts, the more work required to accurately process them.
A particularly important aspect is tolerance. Precision machining is always within your tolerance. There is a compliance line between the workpiece, workpiece clamping method, tool and the machine itself. If there is any reduction in stiffness along this path, it may lead to deflection and flutter, resulting in inaccurate dimensions. In order to improve the accuracy of the CNC machining process, please ensure that your system (workpiece, workpiece fixture, tool and machine) is optimized for stiffness.
Why is accuracy important?
In some industries, precision machining may be more important than others. Some parts or products need to be very reliable and work properly every time. Take medical equipment for example. The surgical robot driven by the doctor needs to be executed completely according to the instructions, without hysteresis, sliding or unexpected action. Even “simple” daily blood pressure readings are important for correct diagnosis and need to be correct every time. As far as people’s health is concerned, there is not much room for tolerance.
The automobile industry is another industry that needs precision parts. You want your car to run reliably every day, right? And consumer electronics: You want your phone to open and make calls when needed. Each of these products comes down to the interaction of many parts that need to cooperate and work together. This requires manufacturing precision parts in the same way every time.