There are 16 kinds of surface treatment processes during parts processing after CNC machining&molding, including Grinding, sand blasting, polishing, spraying, powder spraying, UV spraying, printing, radium carving, electroplating, oxidation, passivation, blackening, wire drawing, phosphating, water transfer printing and bronzing.Cnc proto lab offers services of most of them.
Here,we wil talk about these treatments in detail:
1.Grinding: use sandpaper to rub the workpiece surface to remove burrs, machining lines, bonding marks and other defects on the workpiece surface, so as to improve the flatness of the workpiece, reduce roughness, and make the workpiece surface smooth and fine.
2. Sand blasting: the compressed air is used as the power to form a high-speed jet beam to spray the materials (copper ore, quartz sand, carborundum, iron sand, sea sand) to the surface of the workpiece to be treated at a high speed. Due to the impact and cutting effect of the abrasive on the surface of the workpiece, the surface of the workpiece gets a certain degree of cleanliness and different roughness, so that the mechanical properties of the surface of the workpiece are improved, so the fatigue resistance of the workpiece is improved, It increases the adhesion between the workpiece and the paint coating, prolongs the durability of the paint film, and is also conducive to the leveling and decoration of the paint.
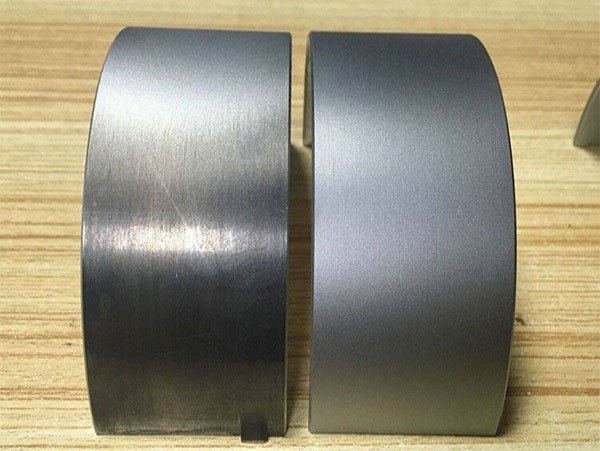
3. Polishing: the surface of the workpiece is modified by using flexible polishing tools, abrasive particles or other polishing media on the basis of desert. Polishing cannot improve the dimensional accuracy or geometric shape accuracy of the workpiece, but aims to obtain a smooth surface or mirror luster, and sometimes it is also used to eliminate luster (matting). The surface roughness of the workpiece after polishing can generally reach Ra0.63-0.01 μ m. PMMA transparent parts require very high polishing requirements, so the price of PMMA transparent parts is very expensive, more than 4 times that of ordinary ABS parts.
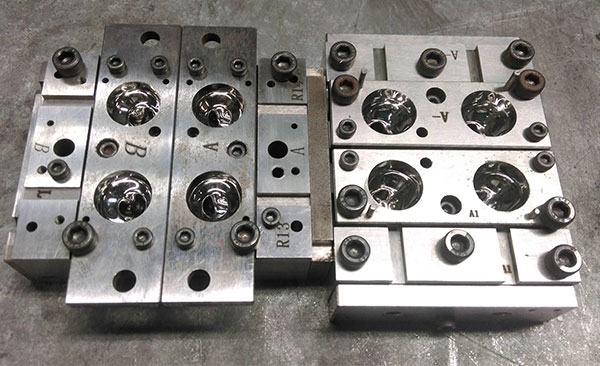
4. Spraying: surface painting is one of the most widely used surface processes.
Spraying has the following advantages:
(1) It can cover the surface defects of the workpiece after forming
(2) The workpiece surface can be painted to obtain various colors, different glossiness, different visual effects and different handfeel
(3) The hardness and scratch resistance of the workpiece surface are enhanced. The spraying effects include: matte, semi matte, bright (high gloss), various colors, various textures, etched lines, wire drawing effect (wire drawing can only be done with metal colors), leather effect, elastic feel effect (rubber paint), etc.
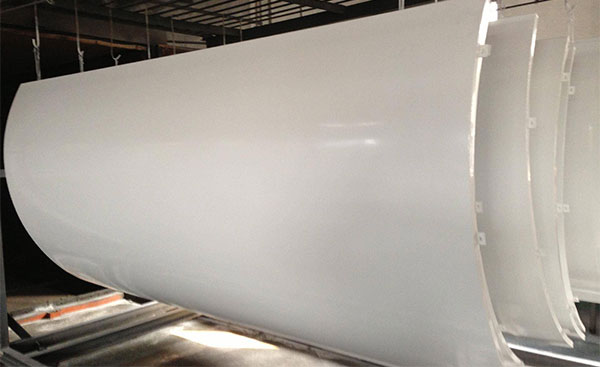
5. Plastic spraying (powder spraying): Electrostatic plastic spraying uses corona discharge to adsorb the powder on the workpiece. The process is as follows: the powder coating is fed into the spray gun by the powder supply system through compressed air. The high voltage generated by the high-voltage electrostatic generator is added at the front end of the spray gun. Due to corona discharge, dense charges are generated near the gun. When the powder is sprayed from the gun nozzle, charged coating particles are formed. Under the effect of static electricity, it is absorbed to the workpiece with opposite polarity. With the increase of powder sprayed, the charge accumulation is more, When it reaches a certain thickness, due to electrostatic repulsion, it is no longer adsorbed, so that the whole workpiece can obtain a powder coating of a certain thickness, and then the powder is melted, leveled and solidified by heat, that is, a silhouetted coating film is formed on the surface of the workpiece. Advantages and disadvantages of electrostatic powder spraying: no thinner, no poison, no pollution to the environment, good coating quality, very high adhesion and mechanical strength, corrosion resistance, short curing time, no primer, low technical requirements for workers, high powder recycling rate, thick coating, wavy and uneven surface effect, only semi matte and bright appearance effects can be processed.
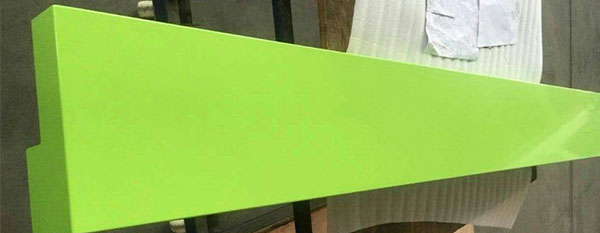
6. UV spraying: the board surface is protected by UV treatment. UV is UltraViolet. UV paint is UV curing paint, also known as light triggered paint.
Advantages and disadvantages of UV:
(1) High hardness. The highest hardness can reach 5-6H
(2) Fast curing speed and high production efficiency. It can be cured in 30 minutes through ultraviolet curing
(3) The coating has excellent performance. The coating has very high performance indicators in terms of hardness, wear resistance, acid and alkali resistance, salt spray resistance, gasoline resistance and other solvents, especially the plump and shiny paint film
(4) The UV curing process used for UV paint is pollution-free when painting, and is recognized as a green environmental protection product
(5) UV paint is sensitive to ash production, so it has strict requirements on the construction environment
(6) It is easy to burst during spraying
(7) It is not protected from the sun and is easy to crack under the sun
(8) It will turn yellow after a long time. Therefore, UV glazing is generally not used when the product appearance requires pure white
(9) The price is expensive, and the requirements for coating pretreatment are very high.
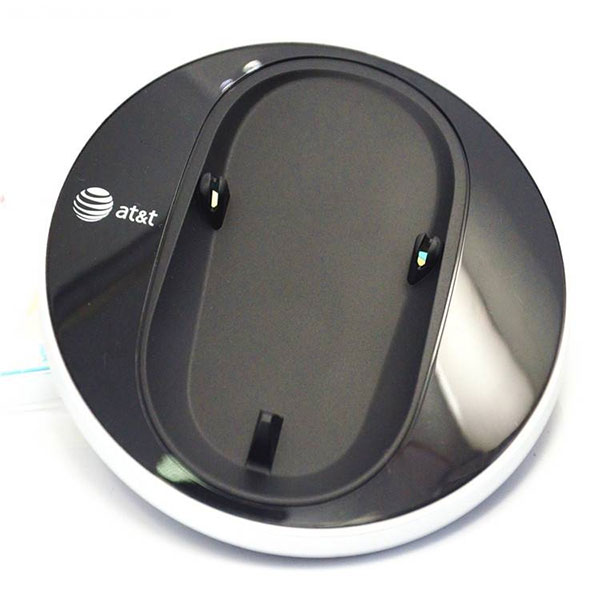
7. Print:
(1) Wire mesh
Part of the mesh of the printing plate can pass through the ink and miss printing on the substrate. The mesh of the rest of the printing plate is blocked and cannot pass through the ink. A blank is formed on the substrate. The mesh of the part to be inked on the printing plate is not closed. During printing, the ink passes through and forms ink on the substrate. During printing, ink is poured into one end of the screen printing plate. The ink will not leak on the substrate through the mesh without external force, When the ink is scraped by the ink scraper with a certain angle and pressure, the ink is transferred to the substrate under the screen plate through the screen plate, so as to achieve image reproduction (the printed pattern is convex)
Advantages of silk screen printing:
A. Low cost, see the effect
B. Suitable for printing on irregular substrate surface
C. Strong adhesion and good inking
D. Thick ink layer with strong stereoscopic effect
E. Strong optical rotation resistance and good color formation
F. Wide range of printing objects and large printing format
Advantages of silk screen printing:
A. Low cost, see the effect
B. Suitable for printing on irregular substrate surface
C. Strong adhesion and good inking
D. Thick ink layer with strong stereoscopic effect
E. Strong optical rotation resistance and good color formation
F. Wide range of printing objects and large printing format
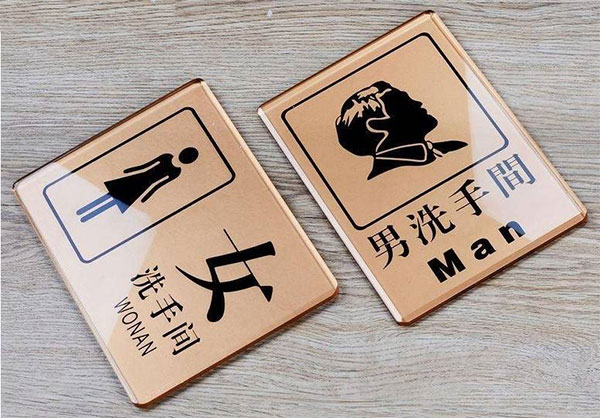
(2) Transfer printing (curved surface printing): It refers to printing the words and patterns to be printed on the surface of plastic molding products with curved or slightly concave convex surfaces with a piece of flexible rubber. Transfer printing is to put the ink into the intaglio with engraved words or patterns, then copy the words or patterns onto the rubber, transfer the words or patterns onto the surface of plastic molding products with rubber, and finally solidify the ink by heat treatment or ultraviolet light irradiation.
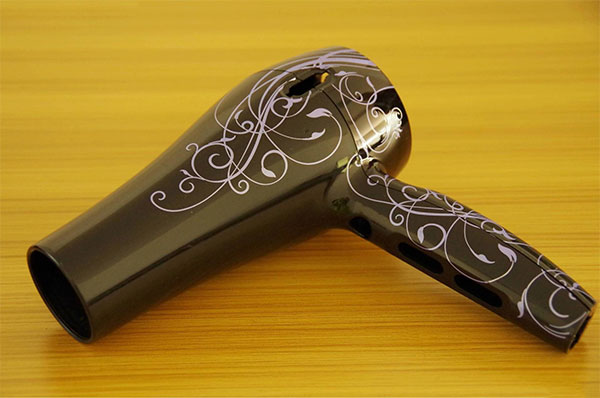
8. Radium carving: also known as laser carving, it is a process of surface treatment using optical principles. For example, if you want to build a keyboard, it has blue green, red, and gray on it, and the body is white. When laser engraving, you should first spray oil with corresponding colors for blue characters, green characters, red characters, and gray characters, so that it looks like there are blue keys, green keys, and other keys, and then spray a layer of white on the whole. This is a whole white keyboard, and all blue and green characters are wrapped under it. Then, the film is made of laser technology and the key map submitted by the industrial designer. The white oil on the film is carved out to show blue and green buttons.
Limitations of radium carving:
(1) Reviewed by laser carving: AL is 0.1mm, plastic paint coating: 0.2-0.3mm. Iron and other metals up to 0.08mm
(2) The limit surface area of the radium carving is 100 * 100mm. If it exceeds 100 * 100mm, the radium carving needs to be spliced. The connection position is not beautiful and the connection trace is obvious
(3) White and near white colors cannot be carved, and characters carved from curved radium are prone to deformation
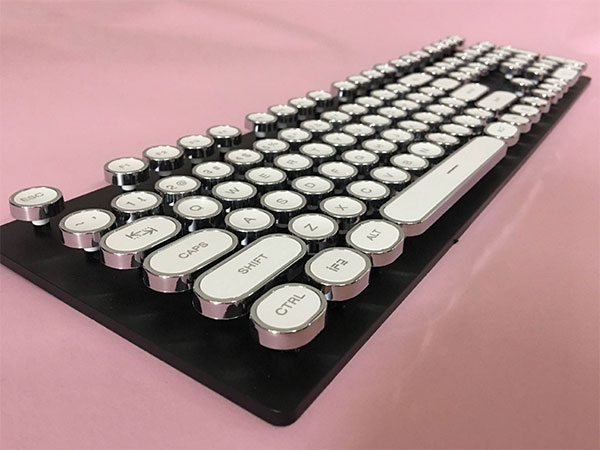
9. Electroplating: Does electroplating use electrodes to pass current to make metal adhere to the surface of an object? Its purpose is to change the characteristics or size of the object surface. Electroplating is generally divided into wet electroplating and dry electroplating. The wet method is commonly referred to as water plating, while the dry method is commonly referred to as vacuum plating. Water plating is to generate ion replacement and attach the coating metal to the surface of the plating piece through the electrode method. The vacuum plating is to use high voltage and large current to make the coating metal instantly vaporize into particles under the vacuum environment and then evaporate to the surface of the plating piece. The water plating adhesion is good, and no other treatment is required later. The vacuum plating adhesion is poor, and generally needs to do PU or UV on the surface, The PC cannot be plated. The laminating parts can only be vacuum plated instead of water plated. The color of water electroplating is monotonous. Common water electroplating includes chromium, nickel, gold, etc., while vacuum electroplating can solve the problem of colorful colors. Before water electroplating, the surface effect of the workpiece must be polished to 1500-2000 sandpaper, and then polishing can be used for water electroplating. Therefore, the work of water electroplating is generally very expensive, and the effect of vacuum plating can be slightly less than 800-1000 sandpaper, so vacuum plating is relatively cheap.
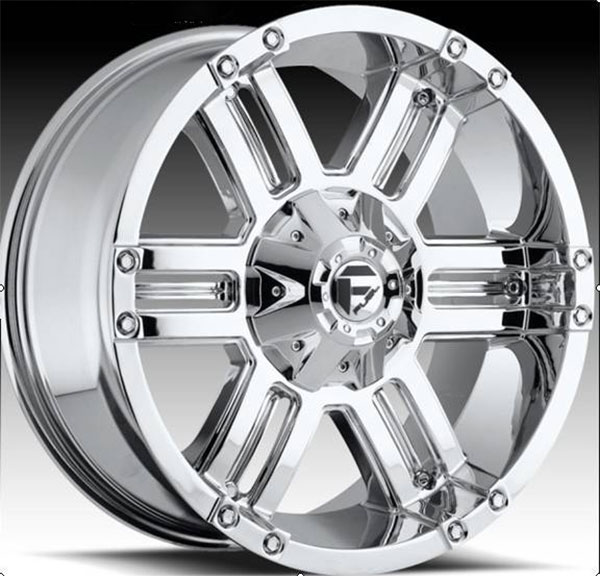
10. Oxidation: The oxidation treatment of metal is to form a protective oxide film on the metal surface by acting with oxygen or oxidant, which imitates metal corrosion. Oxidation is divided into chemical oxidation and electrochemical oxidation (i.e. anodic oxidation).
(1) The oxide film produced by chemical oxidation is thin, about 0.3-4vm thick, porous, with good adsorption capacity, soft and non wear-resistant, and good conductivity. It is suitable for occasions with shielding requirements. It can be painted with various colors, and its surface can be repainted, which can effectively improve the corrosion resistance and decoration of aluminum products.
(2) The oxide film produced by anodic oxidation is relatively thick, with a thickness of 5-20 vm in general. The thickness of hard anodic oxide film can reach 60-2500 vm. It has high hardness, good wear resistance, good chemical stability, good corrosion resistance, good adsorption capacity, good insulation performance, strong thermal insulation and heat resistance, and can be used in various colors.
To sum up, after chemical oxidation treatment, especially anodic oxidation treatment, the oxide film formed on the surface of aluminum and aluminum alloy has good protection and decorative lamp characteristics, so it is used in aviation, electrical, electronic, mechanical manufacturing and light industry.
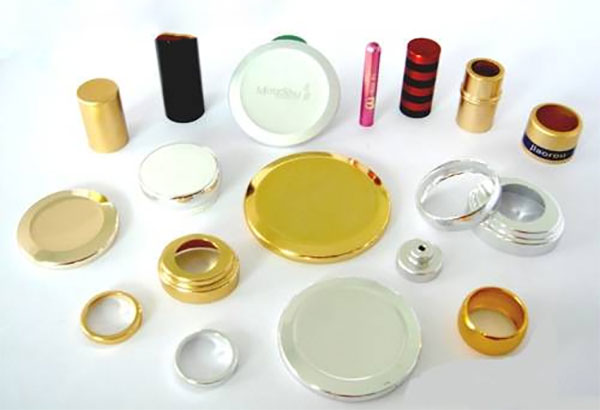
11. Passivation: Under certain conditions, when the potential of metal moves to the positive direction due to the external anode current or local anode current, the state of the originally actively dissolved metal surface will change suddenly. The dissolution rate of metals drops rapidly. This sudden change of surface state is called passivation. Passivation can improve the passivation performance of metal materials, promote the passivation of metal materials in the use environment, and improve the mechanical strength of metal. It is one of the most effective ways for corrosion control, and enhances the adhesion between metal and film.
12. Blackening: surface blackening treatment is also called bluing. There are two commonly used methods for blackening treatment: traditional alkaline heating blackening and late room temperature blackening. The protective film obtained by blackening is black, which improves the corrosion resistance and mechanical strength of the metal surface, and can also be used as a good bottom layer of the paint. (The stainless steel cannot be blackened, and the blackening effect of iron is the best)
13. Wire drawing: wire drawing is a surface treatment method that forms lines on the workpiece surface by grinding products to achieve decorative effect. Wire drawing can well reflect the texture of metal materials, and can make the metal surface obtain non mirror metallic luster. According to different surface effects, it can be divided into straight silk (hair texture) and messy silk (snowflake texture). According to the requirements of wire drawing effect and the size and shape of different workpiece surfaces, wire drawing can be divided into manual wire drawing and mechanical wire drawing. Common manual wire drawing is mostly used for 3M company’s industrial cleaning cloth. Good tea sets with silk patterns are subjective. Each user has different requirements for surface lines and different preferences for line effects. Therefore, it is necessary to have a drawing template to produce a satisfactory effect. The circular arc (the junction between the curved surface and the straight surface is very unsightly, and the wire drawing is uneven) and the paint surface (the metal color surface can be used to draw fine silk lines) should not be drawn.
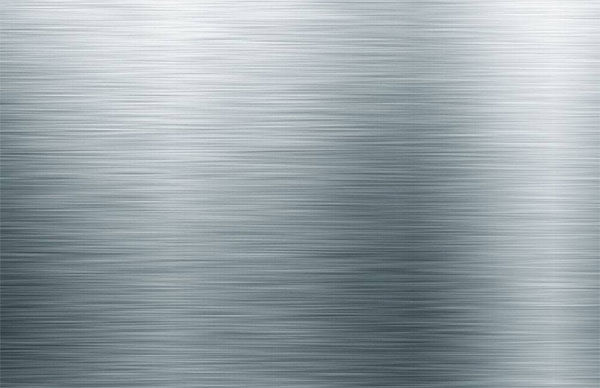
14. Phosphating: surface phosphating is the process of treating metal surface with orthophosphate solution of manganese, zinc, iron and other metals to form an insoluble phosphate protective film. The protective film generated after phosphating treatment can improve the metal insulating shoes and corrosion resistance, improve the protection and decoration performance of the workpiece, and can also be used as a good primer of the paint. The phosphating treatment of metal surface can be divided into cold phosphating (room temperature phosphating), hot phosphating, spray less phosphating and electrochemical phosphating. Phosphating treatment is the main method for pretreatment of painted parts such as automobile panels, cabs and trunk plates in the automobile industry. It requires that the phosphating film be fine, smooth, uniform, of moderate thickness and of certain heat resistance.
15. Water transfer printing: Water transfer printing technology is a kind of printing that uses water pressure to hydrolyze the transfer paper/plastic film with color patterns into polymers. There are two types of water transfer technology, one is water mark transfer technology, the other is water drape transfer technology. The former mainly completes the transfer of words and realistic patterns, while the latter tends to complete the transfer of the entire product surface. The Cubic Transfer technology uses a water-based film that is easy to dissolve in water to carry images and texts. Due to the excellent tension of the water coating film, it is easy to wind on the product surface to form a graphic layer, and the product surface will get a completely different appearance just like painting. Covering any shape of workpiece, it can solve the problem of three-dimensional product printing for manufacturers. Curved surface coating can also add different lines on the product surface, such as leather lines and wood lines Jadeite pattern and marble pattern can also avoid the virtual position often seen in general page printing. In the printing process, since the product surface does not need to contact with the printing film, it can avoid damaging the product surface and its integrity.
Water transfer printing The film with special chemical treatment is printed with the required color lines and then sent to the surface of the water. With the effect of water pressure, the color lines and patterns are uniformly transferred to the surface of the product. When the film is coated, it is automatically dissolved in water. After cleaning and drying, a layer of transparent protective coating is applied. At this time, the product has presented a completely different visual effect.
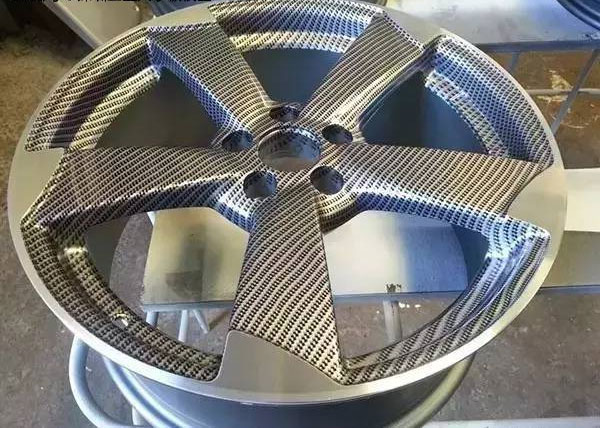
16. Stamping: it refers to pasting gold or silver product color on some details of the product.
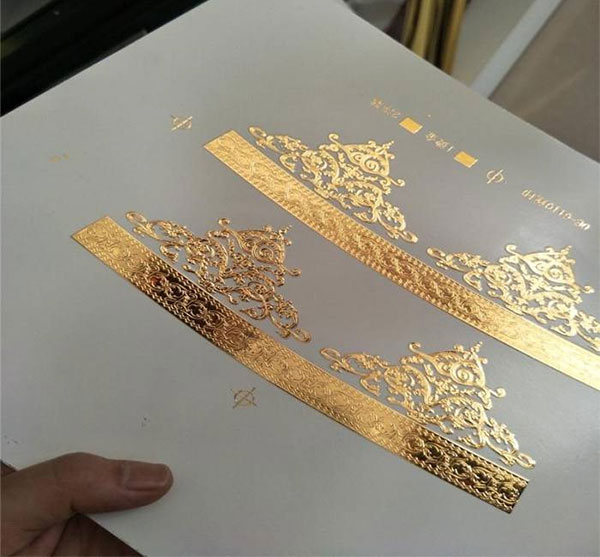
Shenzhen QiYa industrial cnc proto lab offer services of the preliminary development to assist the R&D Department. CNC protolab provides rapid manufacturing of single and small batch products with demands, such as prototyping, RP rapid prototyping sample, rapid mold injection, 3D printing rapid prototyping sample, CNC machining molding sample, vacuum laminating, sheet metal parts, forging parts, plastic parts, exhibition machine display pieces, etc. Industry scope: robots, unmanned aerial vehicles, household appliances, automobile industry, medical machinery, aerospace ships, etc.